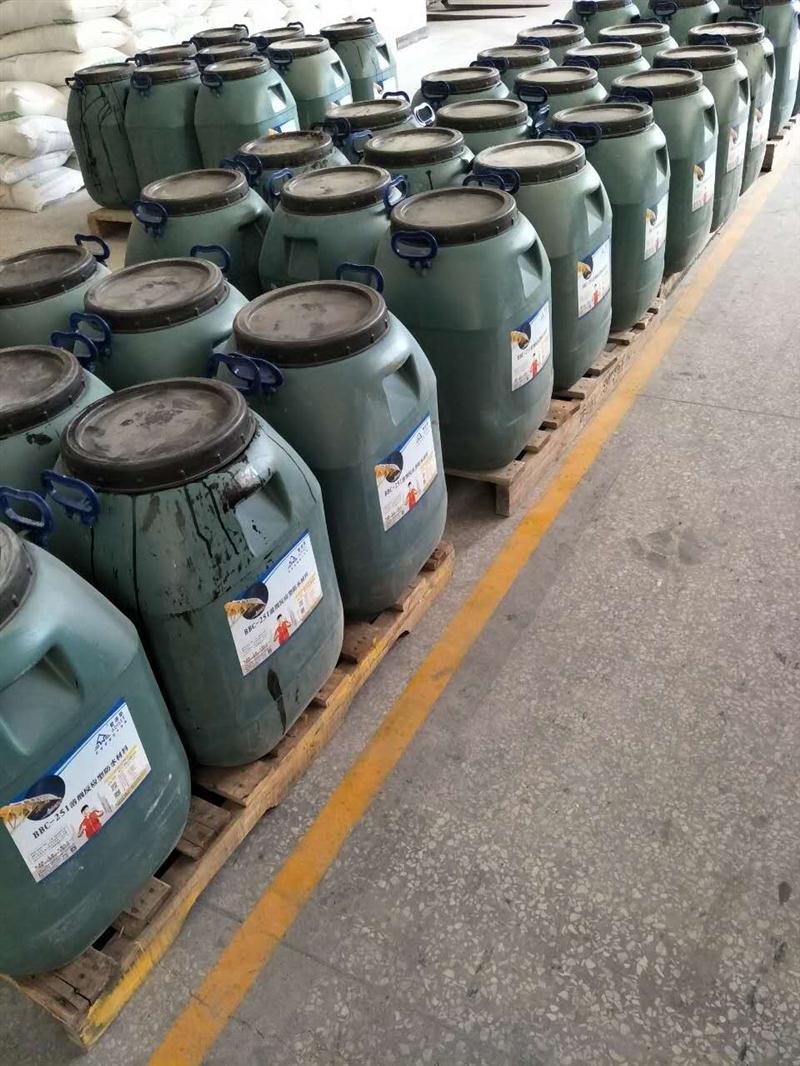
25.220.6023.040.1094备案号:16435-2005中华人民共和国石油天然气行业标准SY/T4106-2005管道无溶剂聚氨醋涂料内外防腐层技术规范Technicalstandardnon一solventpolyurethaneInternalexternalcoatingpipeline2005一07一26发布2005一11-01实施国家发展和改革委员会4106-20051010范围工艺适用性试验表面预处理内防腐层补口..外防腐层补口安全、卫生和环境保护4106-2005本标准是根据石油工业标准化技术委员会秘书处油标委秘字仁2004]12号文件的要求,由天津大港油田浦海化工有限公司和中国石油天然气集团工程技术研究院编制的。本标准在编制过程中,编制组成员遵照国家有关的方针政策,基于无溶剂聚氨醋涂料内外防腐层技术在国内的应用情况,结合当前涂料施工技术的发展,进行了广泛的调查研究,认真总结了无溶剂聚氨醋涂料内外防腐层在设计、预制、施工及验收方面的实践经验,并参考了德国标准DIN30671《敷设于地下的钢管的热固性塑料涂层(外涂层)》和美国水工协会标准ANSI/AWWAC222-1999《钢制水管管件聚氨醋内外涂层》的有关内容,形成了征求意见稿,又以多种方式广泛征求有关单位和专家的意见,对本标准的主要内容进行了反复修改,最后由石油工程建设施工专业标准化委员会会同有关部门进行审查定稿。
本标准的主要内容有:范围,规范性引用文件,总则,内外防腐层的厚度,材料,涂敷工艺,质量检验,防腐层修复涂料品牌网,标识、储存、堆放和运输,现场补口,安全、卫生和环境保护,交工资料等。本标准由天津大港油田浦海化工有限公司提出。本标准由石油工程建设施工专业标准化委员会归口。本标准起草单位:天津大港油田浦海化工有限公司、中国石油集团工程技术研究院。本标准主要起草人:SY广r4106-2005管道无溶剂聚氨醋涂料内外防腐层技术规范范围本标准规定了管道无溶剂聚氨醋涂料内外防腐层的设计、施工与验收。本标准适用于:输送介质为原油及成品油、水、天然气且温度不大于90的钢质和铸铁管道无溶剂聚氨醋涂料内防腐层的设计、施工与验收。使用温度不大于100的埋地和表层涂敷抗紫外线涂层的地上钢质和铸铁管道无溶剂聚氨醋涂料外防腐层的设计、施工与验收。规范性引用文件下列文件中的条款通过本标准的引用而成为本标准的条款。凡是注日期的引用文件,其随后所有的修改单(不包括勘误的内容)或修订版均不适用于本标准,然而,鼓励根据本标准达成协议的各方研究是否可使用这些文件的最新版本。凡是不注日期的引用文件,其最新版本适用于本标准。GB/1034塑料吸水性试验方法GB/固体绝缘材料电气强度试验方法工频下的试验GB/T1410固体绝缘材料体积电阻率和表面电阻率试验方法GB/T1725徐料固体含量测定法GB/T1728漆膜、腻子膜干燥时间测定法GB/T1763漆膜耐化学试剂性测定法GB/T1768漆膜耐磨性测定法GB/T1771色漆和清漆、耐中性盐雾性能的测定GB/T2411塑料邵氏硬度试验方法GB6514涂装作业安全规程涂漆工艺安全及其通风净化GB/T6750色漆和清漆密度的测定GB7692涂装作业安全规程涂漆前处理工艺安全及其通风净化GB/T8923涂装前钢材表面锈蚀等级和除锈等级GB/T9751涂料在高剪切速率下粘度的测定GBJ87工业企业噪声控制设讣规范GBZ工业企业设计卫生标准SY/0315-97钢质管道熔结环氧粉末外涂层技术标准为确保管道无溶剂聚氨醋涂料内外防腐层质量,减少输送介质的二次污染,延长管道使用寿命,制定本标准。
3.2本标准所指的聚氨醋徐料应为均匀液状,通常包含两种组分,A组分主要是多异氰酸醋(MDD,B组分主要是多元醇(POLYOL),两组分经反应形成防腐层。3.3管道无溶剂聚氨醋涂料内外防腐层的设计、施工与验收除应执行本标准外,尚应符合国家现行有关强制性标准(规范)的规定。SY/4106-2005内外防腐层的厚度无溶剂聚氨醋涂料内外防腐层的厚度应由设计部门根据管道工程的实际需要确定。当设计无规定时,应符合表防腐厚度内防腐厚度钢管500t}m妻5001m铸铁管妻650f}m>-10p-管道及管件应有制造厂的出厂质量证明书或检验报告单。涂敷商应对管道及管件进行外观质量检验,外观不合格的不得进行防腐。5.2聚氨酉着涂料5.2.聚氨醋涂料的主要技术指标应符合表2的规定,聚氨醋涂料防腐层的性能指标应符合表3粘度mpa98GB/《30GB/T1720315-97附录阴极剥离(650C12SY/0315-97附录0315-97附录50)涂层无裂纹和分层SY/0315-97附录耐磨性(Cs17砂轮,tkg,1000r)1768SY/4106-2005吸水性(24h)硬度(Shore65GB/电气强度MV20GB/T1408.体积电阻率10´GB/1410耐化学介质腐蚀(1000硫30%氯化钠、30Y,氢氧化钠、号柴油,30d)涂层完17635.2.2聚氨on,涂料应有出厂质量证明书及检验报告、使用说明书、出厂合格证等技术资料。
用于输送饮用水管道内壁或与人体接触的聚氨醋涂料,应有国家认证的检验机构按照国家相关的卫生标准检验并出具适用于饮用水的检验报告等证明文件。5.2.3聚氨醋涂料应包装完好,并在包装上标明涂料制造厂家名称、产品名称、型号、批号、产品数量、生产日期及有效期等。5.2.涂敷商应按涂料制造厂家提供的使用说明书的要求存放聚氨醋涂料。5.2.涂敷商应对每一生产批聚氨酷涂料按表2规定的主要性能进行质量复检。不合格的涂料不应涂敷。工艺适用性试验涂敷生产前,涂敷商应按拟定的生产工艺涂敷试验管段聚氨酯防腐涂料标准,并进行防腐层性能检验,检验项目及性能指标应满足表3号或生产厂改变时,应重新进行工艺适用性试验。在表面预处理前,对海运或长时间存放海边的管材应进行盐分检测聚氨酯防腐涂料标准,盐分超标的管材应冲洗至盐分不超过20mg/除锈前,应先除去任何油脂或其他可溶性污染物质。表面的焊清,突出物、毛刺等影响防腐层质量的不平粗糙物应予挫平或磨平,但不得伤及母材。表面温度应高于露点温度3以上且相对湿度应低于85%方可进行除锈作业。钢材除锈等级应达到GB/T8923中规定的Sa2%级的要求,表面锚纹深度达到40tm除锈合格的表面一般应在8h内进行防腐层的涂敷,如果出现返锈,必须重新进行表面处理。
6.3内外防腐层涂敷6.3.涂敷环境条件:表面温度应高于露点温度30C以上,相对湿度应低于85%方可进行涂敷作业。环境温度与管材温度应维持在涂料制造厂家所建议的范围内。雨、雪、雾、风沙等气候条件下,应停SY/4106-2005止防腐层的露天施工。6.3.2管材的加热:如果需要对被涂敷的管材进行加热时,应限制在涂料制造厂家所规定的温度限 值之内,并保证管材表面不被污染。 6.3.3 涂敷材料的加热: 加热方法及加热温度应依照涂料制造厂家的建议。 6.3.4 涂敷方法: 应按涂料制造厂家的要求进行涂敷,可使用手工徐刷或双组分高压无气热喷涂设 备进行喷涂。 6.3.5 涂敷间隔: 每道防腐层喷涂之间的时间间隔应小于涂料制造厂家的规定值。 6.3.‘ 涂敷厚度未达到规定厚度时,如果未超过涂料制造厂家所规定的可复涂时间,可再涂敷同种涂料以达到规定的厚度,但不得有分层现象。 6.3.6. 已超过涂料制造厂家所规定的可复涂时间的防腐层,必须全部清除干净,重新涂敷。6.3.7 管端预留长度应按照设计要求执行。 检验表面预处理质t 检验 7.1. 在完成表面预处理之后,目视检查管材,应没有任何油脂、锈斑、灰尘、尖锐物或其他异物。
7.1.2 以表面粗糙度测试仪或其他合适的方法检查表面粗糙度。表面粗糙度应每天至少测量一次, 每次测一根管表面的锚纹深度,锚纹深度应达到401m- 100tm. 7.1.3 采用GB/ 8923中相应的照片或标准板进行目视比较,除锈等级应达到Sa2万级的要求。 7.2 涂敷完成后的检验 7.2.1 固化检查: 按涂料制造厂家明确指示的涂料固化所需时间进行固化检查,防腐层不得有未干 硬或粘腻性、潮湿或粘稠区域。 7.2.2 防腐层外观: 全部目视检查,防腐层上不得出现尖锐的突出部、龟裂、气泡和分层等缺陷, 微量凹陷、小点或皱折的面积不超过总面积的10%可视为合格。 7.2.3 防腐层厚度: 用磁性测厚仪逐根测量。内防腐层检测距管口大于150mm范围内的两个截面, 外防腐层随机抽取三个截面。每个截面测量上、下、左、右四点的防腐层厚度。所有结果符合表1 最小厚度要求或设计规定值为合格。7.2.4 防腐层检漏: 采用电火花检漏仪对防腐层进行100%面积检漏。检漏电压为5V/gym,发现漏 点应及时修补。 修补材料应采用管体同种涂料或涂料制造厂家提供或推荐的配套修补材料。8.2 不合格而需要修补的部位应明确标记。
8.3 使用刮刀或喷砂方法除去不合格的防腐层。 8.4 用钢丝刷将缺陷周边防腐层 50mm范围内打磨粗糙。原防腐层应保持清洁、干燥、无尘、无松 脱残余物,无影响防腐层附着力的物质。 8.5 按照涂料制造厂家的要求进行机械喷涂或手工涂敷。 修补后防腐层应按7.2.3和7.2.4 的规定进行厚度和漏点检查,厚度符合要求且没有漏点为合 经质量检验合格的防腐管应在明显处作出合格标识。合格标识应包括生产厂名、产品名称、规SY/ 4106-2005 格、执行标准、生产 日期、检验员编号等内容。 9.2 储存与堆放 9.2.1 防腐层实干后方可堆放,堆放高度应符合设计规定。 2.3防腐管应按规格分类堆放,并有明显标识,堆放时用支垫垫起,并高出地面 l00mm 以上, 防腐管之间应衬以柔性衬垫。 9.2. 防腐管的吊装,应采用尼龙吊带或其他不损坏防腐层的吊具。在防腐管的吊装过程中,应避免撞击和划伤防腐层。 运输防腐管装车必须采用尼龙吊带或专用吊具,保护好防腐层和管口。装车时各层防腐管之间用软垫 垫起,捆绑绳加橡胶护套或捆绑绳与防腐管之间加软垫。在装、卸车过程中,应采取必要的措施,防 止变形和防腐层损伤。
10 现场补口 10.1 内防腐层补口 10.1. 补口前应按选定的补口方法制定相应的补口技术措施和质量要求,并经设计、用户审查批准后方可实施。 10.1.2 以无溶剂聚氨醋涂料作为内防腐层的钢质管道应进行现场内补口。补口材料可采用与管体相 同的涂料或涂料制造厂家推荐的其他补口材料。 10.2 外防腐层补口 10.2.1 表面处理: 首先应除去补口处的泥土、油脂、水、焊渣、灰尘等杂质。采取喷砂除锈方法进 行处理,钢材除锈等级应达到 GB/ 8923中规定的Sat %级的要求,表面锚纹深度达到40rm- 100um。在预留区边缘25mm- 50mm的涂层表面上用钢刷或喷砂方式使其形成粗糙面,做为涂层间 的搭接面。 10.2.2 补口处防腐层涂敷: 如果采用原涂敷涂料进行补口,应按照第6章的方法进行涂敷,补口处 的涂敷厚度应等于或大于管体的涂层厚度。如果采用其他专用补口材料,应经涂料制造厂家和设计认 10.2.3补口质量检查: 按照第7 章的方法检查防腐层外观、厚度、漏点等。 11 安全、卫生和环境保护 11.1 涂敷生产的安全、环保应符合 GB 7692 的要求。 11.2 管道除锈、涂敷生产过程中,各种设备产生的噪音应符合GBJ 87 的有关规定。
11.3 管道除锈、涂敷生产过程中,空气中粉尘含量不得超过 GBZ 的规定。11.4 管道除锈、涂敷生产过程中,空气中有害物质浓度不得超过GB 6514 的规定。 11.5 管道除锈、涂敷生产过程中,所有机械设施的转动和运动部fir 应设有防护罩等保持措施。 12 交工资料 防腐施工结束后,施工单位应向用户提供下列资料: 4106-2005 防腐层质量检测报告和质量证明书。其中,质量证明书内容应包括:工程名称、涂料名称及 型号、产品规格、执行标准、生产厂家等。