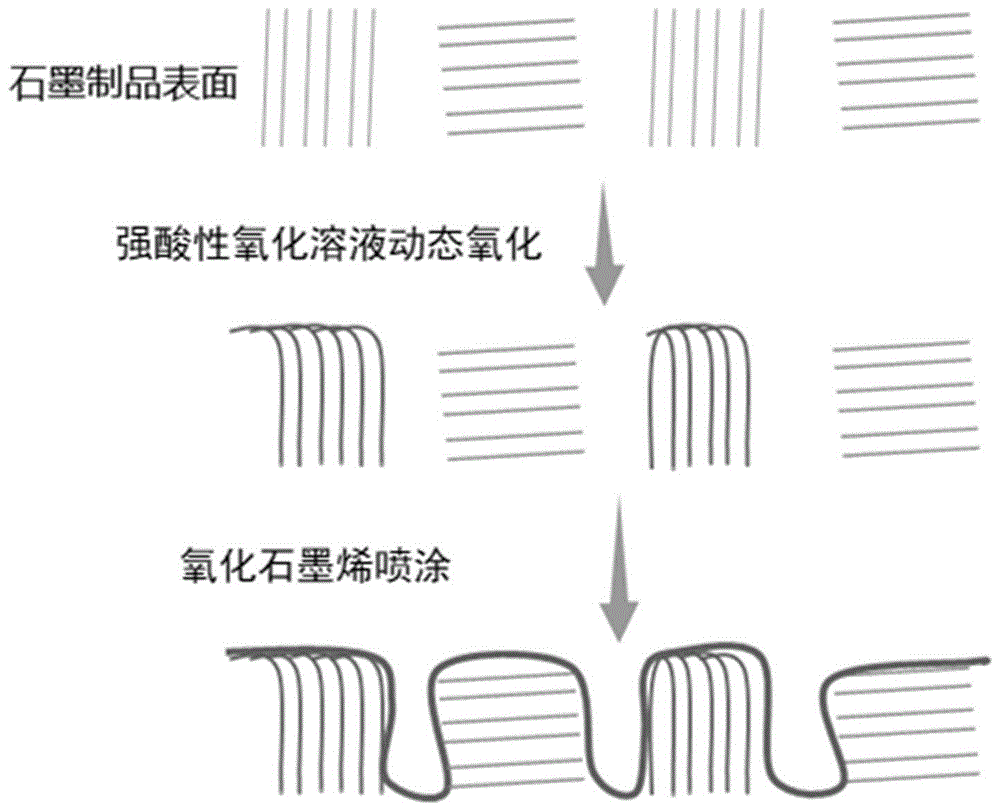
一种石墨制品表面制备纳米石墨涂层的方法
技术领域
本发明属于新材料领域,尤其涉及一种石墨制品表面制备纳米石墨涂层的方法。
背景技术
半导体材料、器件、集成电路的生产和科研已成为电子工业的重要组成部分。用半导体材料制成的部件、集成电路等是电子工业的重要基础产品,在日常生活、军事以及航空航天领域都有极大的用途。
半导体材料的生长都需要高纯净的高温炉来作为生长容器,来保证高温过程中,容器内部气体分子的高度纯净。目前可用的热涂层主要有碳化硅涂层和热沉积石墨涂层两种。但是碳化硅涂层不能耐受长时间的高温过程,特别是2000度以上的过程,其本身也会挥发。热沉积石墨涂层厚度很大,涂层时间长、成本高,容易起皮脱落。
为此,需求一种可以结合两种廉价便捷的涂层制备方法,同时还可以应用在极大的温度范围内。
发明内容
本发明的目的是提供一种石墨制品表面制备纳米石墨涂层的方法,解决现有技术中高温防护性涂层容易挥发造成污染的问题。
本发明的另一个目的是提供一种石墨制品表面制备纳米石墨涂层的方法,该方法采用动态氧化来对石墨制品表面进行活化,动态流动的强酸性氧化溶液使得石墨制品表面的石墨烯层发生顶端溶胀,并随着动态流动的液流取向,提高石墨制品表面氧化石墨烯与喷涂的氧化石墨烯之间的接触面积,从而使得涂层稳定性增加。
本发明的另一个目的是提供一种石墨制品表面制备纳米石墨涂层的方法,该方法采用动态氧化来对石墨制品表面进行活化,以产生大量结合位点与喷涂的氧化石墨烯结合,提高涂层稳定性。
本发明的另一个目的是提供一种石墨制品表面制备纳米石墨涂层的方法,该方法采用动态氧化来对石墨制品表面进行活化,以产生大量结合位点与喷涂的氧化石墨烯结合,这种位点结合构成缺陷,配合高温碳化烧结,伴随缺陷修复,涂层和石墨制品表面形成原子级结合。
本发明的另一个目的是提供一种石墨制品表面制备纳米石墨涂层的方法,该方法采用尺寸分散系数在0.6以上的氧化石墨烯溶液进行喷涂,小片石墨烯可以深入到石墨制品界面的缝隙中,起到填充和铆钉的作用,进一步增强界面稳定性。
本发明采用如下技术方案:一种石墨制品表面制备纳米石墨涂层的方法,该方法包括:
(1)对石墨制品表面进行动态氧化处理,具体为,将所述石墨制品表面浸没在动态流动的强酸性氧化溶液中;其中,所述的强酸性氧化溶液是A和B的硫酸溶液,其中B是氧化物,A是B的高氧化物或过氧化物,硫酸和A的体积质量比介于60mL:1g~0.1g之间,A和B的质量比1:2~1:5之间,氧化时间为10min-30min。
A和B包括:高锰酸钾和二氧化锰;高铁酸钾和二氧化铁;双氧水和水。
(2)用去离子水清洗后,表面喷涂氧化石墨烯溶液成膜,膜的厚度小于100nm。所述氧化石墨烯溶液中的氧化石墨烯的尺寸为10~100u m,分散系数在0.6以上。
(3)晾干后,150摄氏度烧结1小时,然后置于高温炉中高温碳化。
进一步地,步骤1中,所述的强酸性氧化溶液是过氧化物或者高氧化物以及对应氧化物的硫酸溶液,其中过氧化物或者高氧化物可为双氧水、高锰酸钾、高铁酸钾涂料品牌网,对应氧化物为水、二氧化锰、氧化铁,硫酸和高氧化物体积质量比介于60mL:1g~0.1g之间石墨烯钛纳米防腐涂料,过氧化物和高氧化物的质量比2:1~1:5之间,氧化时间为1min-30min。
进一步地,步骤2中,氧化石墨烯溶液的浓度为10ug-1mg/mL之间,以实现纳米级厚度的石墨烯膜的制备。
进一步地,步骤3中,高温碳化:5℃/min升温至1600℃,1600℃维持4小时,20℃/min升温至2600℃。
本发明所述的石墨制品包括石墨衬底、石墨舟等。
本发明的有益效果在于:纳米涂层结合力紧密,不需要粗糙结构仍可涂敷,涂层厚度可控,纳米涂层厚度小,成本极低。
附图说明
图1为涂层制备原理图;
图2为低密度微晶泄露的涂层;
图3为高密度微晶泄露的涂层;
图4为单位面积内微晶含量的测试装置,其中,1为HOPG制备的密封盖子,2为CVD法制备的纳米厚度石墨薄膜,4为石墨制品,3为石墨制品表面的石墨烯涂层。
具体实施方式
实施例1:
一种石墨制品表面制备纳米石墨涂层的方法,该方法包括:
(1)将1g高锰酸钾、2g二氧化锰溶于60mL质量分数为98%的浓硫酸中,得到强酸性氧化溶液。
将10~100um范围内的大尺寸氧化石墨烯和小尺寸氧化石墨烯按比例混合,配置成氧化石墨烯溶液,使得尺寸的分布系数在0.6以上。
(2)取一具有进出口的方口槽,强酸性氧化溶液从进口-出口循环流动,流速0.1m/s,将石墨制品表面浸没在流动的强酸性氧化溶液中,浸泡30min。
(3)用去离子水清洗后,表面喷涂10ug/mL的步骤1配制的氧化石墨烯溶液成膜,膜的厚度小于100nm。
(4)晾干后石墨烯钛纳米防腐涂料,150℃烧结1小时,然后置于高温炉中高温碳化;高温碳化温度过程为:5℃/min升温至1600℃,1600℃维持4小时,20℃/min升温至2600℃。
如图1所示,垂直方向的石墨顶端因为动态氧化和氧化膨胀的原因,发生了沿涂层方向的局部取向,使得涂层可以和制品表面石墨有极好的贴合性和黏附效果;同时小尺寸的石墨烯有利于降低溶液粘度,使得溶液可以渗透到石墨晶粒间隙,增加接触面积和附着力。
对比例1-1
同实施例1,区别在于,步骤2采用plasma等离子体处理方法,对石墨制品表面进行氧化处理。
对比例1-2
同实施例1,区别在于,步骤2采用静态的强酸性氧化溶液进行氧化处理。
对比例1-3
同实施例1,区别在于,步骤3采用较为均一尺寸(分布系数0.3)的氧化石墨烯溶液进行喷涂。
所述耐烧结次数测试方法:将有涂层的制品放于2600℃的环境下,烧结2小时,降温后进行下一次烧结。耐烧结次数为直到涂层结构破坏或挥发微晶数据超标的极限次数。涂层结构破坏是指:裂痕长度大于0.1mm。挥发微晶数据超标是指:每平方厘米中,挥发微晶数量大于100个。
单位面积内微晶含量的测试方法为:将CVD法制备纳米厚度石墨薄膜铺设在待测样品表面(含有石墨烯涂层的一面),用HOPG制备密封盖子,四周压住CVD法制备的纳米厚度石墨薄膜;如图4。2600℃烧结2小时。通过扫描电镜的标定方法,检测CVD法制备的纳米厚度石墨薄膜下表面的单位面积的微晶数量。
实施例2:
一种石墨制品表面制备纳米石墨涂层的方法,该方法包括:
(1)将1g双氧水、5g水溶于600mL质量分数为98%的浓硫酸中,得到强酸性氧化溶液。
将10~100um范围内的大尺寸氧化石墨烯和小尺寸氧化石墨烯按比例混合,配置成氧化石墨烯溶液,使得尺寸的分布系数在0.6以上。
(2)取一具有进出口的方口槽,强酸性氧化溶液从进口-出口循环流动,流速0.1m/s,将石墨制品表面浸没在流动的强酸性氧化溶液中,浸泡10min。
(3)用去离子水清洗后,表面喷涂1mg/mL的步骤1配制的氧化石墨烯溶液成膜,膜的厚度小于100nm。
(4)晾干后,150℃烧结1小时,然后置于高温炉中高温碳化;高温碳化温度过程为:5℃/min升温至1600℃,1600℃维持4小时,20℃/min升温至2600℃。
对比例2-1
同实施例2,区别在于,步骤2采用plasma等离子体处理方法,对石墨制品表面进行氧化处理。
对比例2-2
同实施例2,区别在于,步骤2采用静态的强酸性氧化溶液进行氧化处理。
对比例2-3
同实施例2,区别在于,步骤3采用较为均一尺寸(分布系数0.2)的氧化石墨烯溶液进行喷涂。
实施例3:
一种石墨制品表面制备纳米石墨涂层的方法,该方法包括:
(1)将1g高铁酸钾、4g氧化铁溶于100mL质量分数为98%的浓硫酸中,得到强酸性氧化溶液。
将10~100um范围内的大尺寸氧化石墨烯和小尺寸氧化石墨烯按比例混合,配置成氧化石墨烯溶液,使得尺寸的分布系数在0.6以上。
(2)取一具有进出口的方口槽,强酸性氧化溶液从进口-出口循环流动,流速0.1m/s,将石墨制品表面浸没在流动的强酸性氧化溶液中,浸泡20min。
(3)用去离子水清洗后,表面喷涂0.5mg/mL的步骤1配制的氧化石墨烯溶液成膜,膜的厚度小于100nm。
(4)晾干后,150℃烧结1小时,然后置于高温炉中高温碳化;高温碳化温度过程为:5℃/min升温至1600℃,1600℃维持4小时,20℃/min升温至2600℃。
所得产品耐烧结次数为57和单位面积内微晶含量为21。
实施例4:
一种石墨制品表面制备纳米石墨涂层的方法,该方法包括:
(1)将将1g高锰酸钾、2g二氧化锰溶于80mL质量分数为98%的浓硫酸中,得到强酸性氧化溶液。
将10~100um范围内的大尺寸氧化石墨烯和小尺寸氧化石墨烯按比例混合,配置成氧化石墨烯溶液,使得尺寸的分布系数在0.6以上。
(2)取一具有进出口的方口槽,强酸性氧化溶液从进口-出口循环流动,流速0.1m/s,将石墨制品表面浸没在流动的强酸性氧化溶液中,浸泡10min。
(3)用去离子水清洗后,表面喷涂1mg/mL的步骤1配制的氧化石墨烯溶液成膜,膜的厚度小于100nm。
(4)晾干后,150℃烧结,然后置于高温炉中高温碳化;高温碳化温度过程为:5℃/min升温至1600℃,1600℃维持4小时,20℃/min升温至2600℃。
所得产品耐烧结次数为61和单位面积内微晶含量为9。