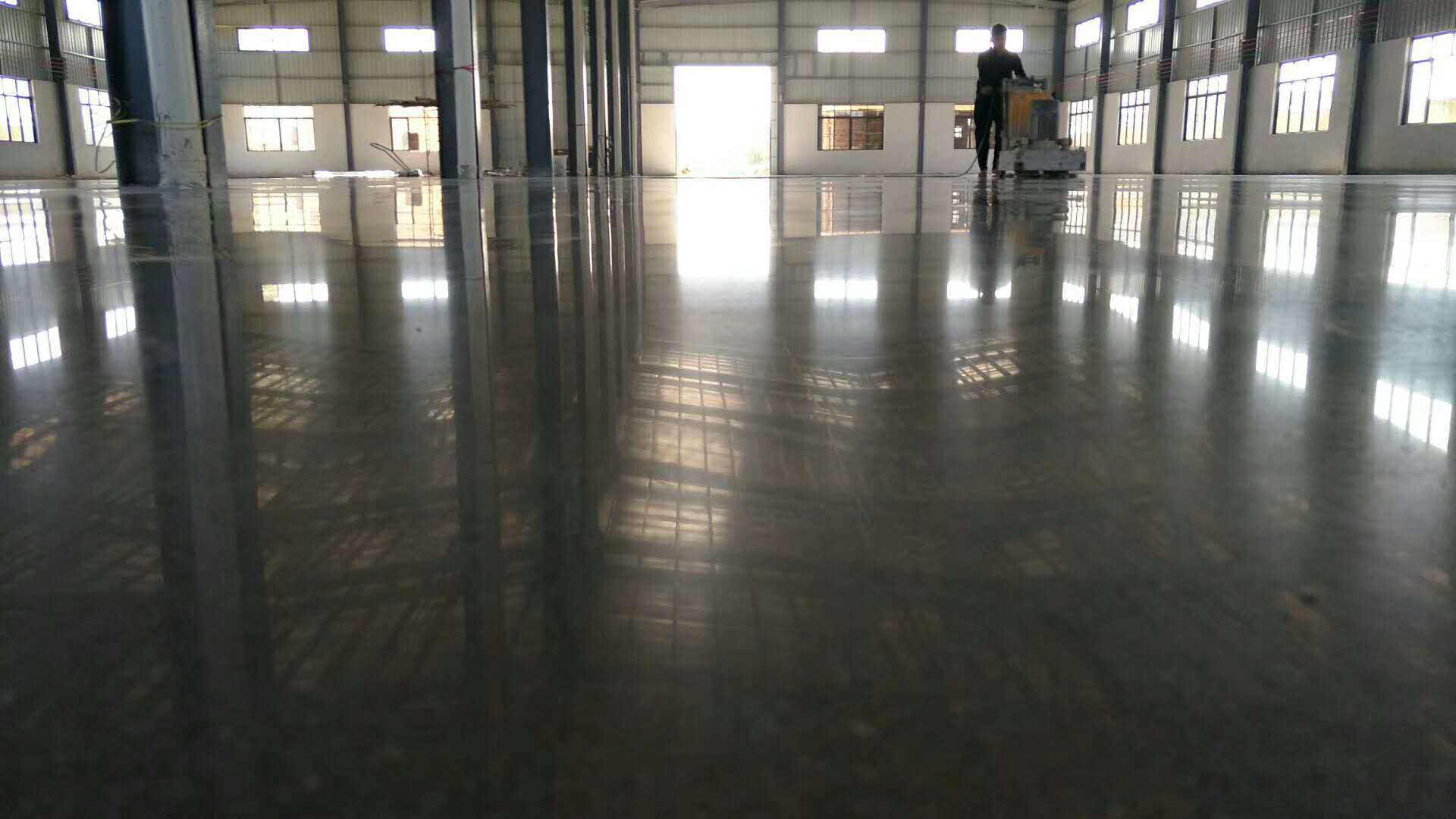
韦代东 weidaidong15@mails.ucas.ac.cn
引用本文:
韦代东, 曾娟娟, 陈海基. 高渗透性环氧树脂防水防腐涂料的制备及性能[J]. 中国塑料, 2021, 35(2): 8-13.
WEI Daidong, ZENG Juanjuan, CHEN Haiji. Preparation and Performance of High Permeable Epoxy Waterproof and Anticorrosive Coating[J]. China Plastics, 2021, 35(2): 8-13.
前言
混凝土是一种多孔性介质材料,在使用过程中腐蚀因子往往能够通过混凝土中的微细裂缝渗透于混凝土内部,日积月累后,对混凝土结构造成严重的腐蚀破坏。因此对混凝土表面涂刷涂料以提高其防水防腐性能、减缓劣化进程,是延长其使用年限的一项重要手段。
随着地下隧道、地铁事业的蓬勃发展,盾构预制混凝土管片的使用越来越普遍。我国地铁设计规范中明确提出了100年的设计寿命,因此,要确保地铁的百年寿命必须要解决地下混凝土结构的防腐防水问题。环氧树脂具有优异的粘接性能和力学性能,固化收缩率低的特点,广泛应用于化学灌浆、涂料、地坪涂装和船舶防腐等 。高渗透性环氧涂料既可以渗透到混凝土结构内部又可以在表面形成一层保护膜,它改变了涂料与混凝土基面的粘接方式能与无机混凝土材料形成“植根式”的交错结构,消除两者之间的温变系数差异较大产生的应力集中而导致疲劳脱落的问题。目前,对高渗透性环氧涂料的研究中,关于助剂对其成膜情况的影响及其作为涂料在不同强度等级混凝土的渗透深度情况仍鲜有报道。
糠醛和丙酮在一定条件下能相互反应,不仅能极大地降低环氧树脂的黏度,还可以对环氧树脂起到增韧作用。糠醛-丙酮-环氧树脂体系固结体的性能不但与三者之间的配比有着密切联系,还与固化剂、促进剂的用量息息相关。本文以糠醛和丙酮作为环氧树脂的活性稀释剂,以酚醛改性胺为固化剂,以DMP-30为固化促进剂辅以成膜助剂制备一种高渗透性环氧树脂涂料用于地下混凝土构件表面防水防腐。分析了该高渗透性环氧涂料的反应机理,考察了其成膜情况及其在不同强度等级的混凝土构件表面的渗透深度。
样品制备
A组分的制备:将环氧树脂E51、糠醛、丙酮按(40~60):(20~40):(20~40)的质量比混合搅拌均匀,再加入0.1 %(质量分数互穿网络防腐涂料国家标准,下同)的助剂得到A组分;
B组分的制备:B组分由90 %的酚醛改性胺固化剂和10 %的DMP⁃30组成;
高渗透性环氧树脂防腐防水涂料的制备:将A、B组分按10∶1的质量比配料,搅拌3~5 min即得到高渗透性环氧树脂防腐防水涂料,所制备涂料在温度为(23±2) ℃,相对湿度为(50±10) %条件下固化168 h后进行性能测试。
结果与讨论
1. 固化机理分析
高渗透性环氧树脂固化体系中环氧、丙酮、糠醛和胺类化合物两两之间能发生缩合反应。糠醛和丙酮、糠醛自身、丙酮自身都能聚合生成复杂的呋喃树脂与环氧树脂固化后能形成互穿网络结构, 兼具环氧树脂和呋喃树脂的优良性能,如抗压强度高、耐水、耐酸、耐碱、耐老化性能出众等。当A和B组分混合后反应立即发生。糠醛和胺之间首先起反应[图1(a)],并大量放热,导致浆液迅速升温。大部分的改性胺固化剂与糠醛反应生成醛亚胺,导致参与环氧固化的胺减少,因此固化速度变慢。此外,丙酮也能与胺类反应生成酮亚胺[图1(b)]。组成高渗透涂料的E51、A组分和B组分混合15 min后、固化物的FTIR曲线见图2。由图2可知互穿网络防腐涂料国家标准,E51的FTIR谱图中不存在1 644 cm-1处的酮(醛)亚胺的特征吸收峰,但在涂料反应15 min后及其固化物的FTIR谱图中明显观察到酮(醛)亚胺的吸收峰,证明了活性稀释剂和固化剂反应生成了酮(醛)亚胺。固化物在911 cm-1处对应于环氧基团的吸收峰明显消失了,表明涂料在168 h已固化完全。
图1高渗透性环氧树脂涂料体系的反应机理
图2高渗透环氧涂料固化前后的FTIR谱图
当糠醛和丙酮的摩尔比为2∶1时,主要生成二糠叉丙酮[图1(c)]。当丙酮过量时,糠醛和丙酮进一步反应,生成物中大量的是一糠叉丙酮。此外,醛亚胺是羟醛缩合的有效催化剂,因为醛亚胺易质子化,且质子化后更容易使醛、酮加成,使糠醛和丙酮的缩合反应更容易朝着一个方向进行。糠叉丙酮通过和有机胺反应与环氧树脂键接到一起,改变了环氧树脂的主链结构,形成如图1(d)所示的三维网状结构。该反应使得作为稀释剂的糠醛和丙酮有效地交联到环氧树脂固化物结构中,降低了固化过程中稀释剂的挥发,减小了固化物的收缩性。该高渗透性环氧树脂涂料的固含量高达80 %,远远高于涂料的理论固含量(52 %),表明糠醛、丙酮活性稀释剂和固化剂发生了反应,交联到固化物中。
2.初始黏度分析
浆液的初始黏度直接影响到涂料的流动性及渗透性。如图3(a)所示,涂料浆液的初始黏度为9 mPa·s,表明该活性稀释剂体系对E51具有优异的稀释作用。涂料的温度随时间的变化如图3(b)所示, A、B组分混合后,该体系的温度急剧上升至56 ℃,随后慢慢降低,到60 min后温度再次上升至54 ℃,100 min后温度再次降低。初期的温度急剧上升主要是由于该期间改性胺固化剂在糠醛、丙酮体系中剧烈反应生成了醛亚胺和酮亚胺,使得参加和环氧树脂反应的胺减少了,在一定程度上减缓了固化速率,因而初期的黏度上升较缓慢,涂料有较长的渗透时间。
图3涂料的黏度和温度随时间的变化曲线
3.助剂对涂料成膜性能的影响
助剂的添加量很少,但对涂料的成膜性能影响巨大。助剂对高渗透性环氧树脂涂料在混凝土试块表面的成膜的影响见图4。由图4(a)可见,未添加任何助剂的涂料涂刷于混凝土试块表面的润湿铺展性差,表干后出现成膜不均匀和涂料无法完全遮盖住混凝土试块表面,有大量瑕疵和斑点,严重影响涂料外观和防护性能。尽管糠醛和丙酮作为混合溶剂使得环氧树脂E51在混凝土表面的润湿性得到极大地提高,但是随着涂料固化的进行以及部分溶剂的挥发,涂料体系的表面张力变大,涂料难以完全润湿混凝土表面,因而出现铺展困难,特别是有油渍污点及凹凸不平的地方。为了解决涂料铺展性能差的问题,向A组分中分别添加0.1 % 的wss-313、7001和BYK⁃333改性助剂,其相应的涂料在混凝土表面的成膜情况如图4(b)、(c)、(d)所示。在图4(b)中,添加wss⁃313水性流平剂后涂料未能有效地润湿混凝土,可能是由于该助剂不适用于油性体系,不利于涂料最终防护性能。在添加BYK⁃333流平剂改性后,涂料在混凝土表面上的润湿性能优异,表干后得到平整、光滑的涂层[图4(d)],基本解决了涂料在混凝土表面出现的弊病。不作说明时,后文所制备试样均添加 BYK-333助剂。
图4助剂对涂料在混凝土表面的成膜影响
4.涂刷次数对涂料成膜厚度的影响
由于糠醛-丙酮-环氧体系固化的独特反应机理,其表干时间和实干时间比普通溶剂型涂料的要长,这也使得材料有更加充足的时间渗透于混凝土结构之中。在第1遍涂刷4 h 后重新配制浆液进行第2遍涂刷涂料品牌网,此时,未完全固化的涂料有部分可反应基团能够继续和新刷的涂料进行固化反应,最终能够有效促进2层涂料的结合,以避免在应力状态下涂层由于相容性不足而导致的起皮、脱落、防腐失效等现象,提高了防护涂层的整体质量。如图5所示,涂刷1遍、2遍和3遍后的固化膜厚度约为12、35、74 μm。微观上,涂料的内部结构致密且与混凝土的粘接牢固。
图5涂料涂刷不同次数后的SEM照片
5.不同强度等级混凝土对涂料渗透深度的影响
影响涂料渗透性的决定性因素不仅仅是黏度,文献报道渗透性和浆液与被灌介质(岩土或混凝土)的接触角、被灌介质的表面张力和浆液与被灌介质之间的界面张力有关33,并指出亲和力(F)与浆液在混凝土表面的接触角(θ)与浆液自身的表面张力(R)有关,即F=Rcosθ,说明接触角越小,界面张力越小,渗透性也越好。涂料在混凝土结构中的渗透性能越好,渗透深度越大,越能够封堵混凝土结构内部毛细孔,实现涂层对混凝土结构表层的“植根式”粘接,进一步对混凝土结构表层的微细裂缝进行修复补强。如图6所示,混凝土试块侧剖面颜色较深的部分为涂料渗透所到达之处。结果表明,高渗透性环氧树脂涂料在C30等级混凝土表面涂膜的渗透深度最大,最深可达5 mm [图6(c)];涂料在C40等级混凝土表面涂膜的渗透深度次之[图6(g)];涂料在C50等级混凝土表面涂膜的渗透深度最小。随着混凝土试块强度等级越高,混凝土构件的致密性越高,致使涂料浆液渗入困难。由于混凝土表面的非均质性,涂料渗入深浅不一,渗入与未渗入部分的界面呈一个不规整的、犬牙交错的界面,有助于消除温度变化时在界面上产生的应力集中现象,减少脱皮现象的出现,从而提高混凝土的耐久性。
图6涂料在不同等级混凝土表面的渗透深度
6.耐化学介质性分析
涂料经耐酸、耐碱、耐盐测试后的质量损失率和表面变化情况见表1。由表1可见,该高渗透环氧树脂涂料经耐酸、耐碱、耐盐测试后的质量损失分别为2.92 %、1.94 %、0.88 %,表明固化后的涂料交联密度大、涂层致密,具有优异的阻隔性能。相对于耐碱性和耐盐性,涂层更容易受到酸性物质攻击。涂料在耐酸、耐碱、耐盐测试前后的照片见图7。由图7可知,纤维水泥板上的涂层分别在酸、碱、盐介质中浸泡168 h后均未出现开裂、起皮、剥落现象,表明涂料具有良好的耐化学介质性,能够有效地阻隔酸、碱、盐溶液通过涂层的孔洞渗入混凝土内部腐蚀混凝土,从而提高混凝土的防腐性能。
表1高渗透性环氧树脂防水防腐涂料的耐化学介质性
图7涂料的耐化学介质性
7.其他性能分析
本文所制备的高渗透性环氧防水防腐涂料的一些其他性能如表2所示。涂料的表干时间仅为6 h,实干时间小于12 h。涂料与混凝土板的干基面粘接强度和潮湿基面粘接强度分别达到4.5、3.6 MPa, 达到JC/T 2217—2014《环氧树脂防水涂料》对粘接强度的要求。固化物的抗压强度达到91.7 MPa,表明该涂料渗入混凝土裂缝中将对裂缝具有良好的补强加固效果,能较大幅度提高混凝土的抗裂能力。固化168 h后的凝胶含量达到95.8 %,固化程度较高,固含量达到80 %,吸水率仅为0.21 %。
表2高渗透性环氧树脂防水防腐涂料的其他性能
结论
(1)高渗透性环氧涂料应用于管片防水防腐保护,具有初始黏度低、表干时间较短、成膜性优异、在C30等级混凝土表面的渗透深度可达到5 mm;
(2)涂料固化完全后的凝胶含量达到95.8 %、固含量达到80 %、吸水率仅为0.21 %,粘接强度高、耐水和耐酸、碱性、耐盐性能良好;
(3)高渗透性环氧树脂涂料的固化物的抗压强度达到91.7 MPa,可作为一种“植根式”的混凝土表面增强涂层。