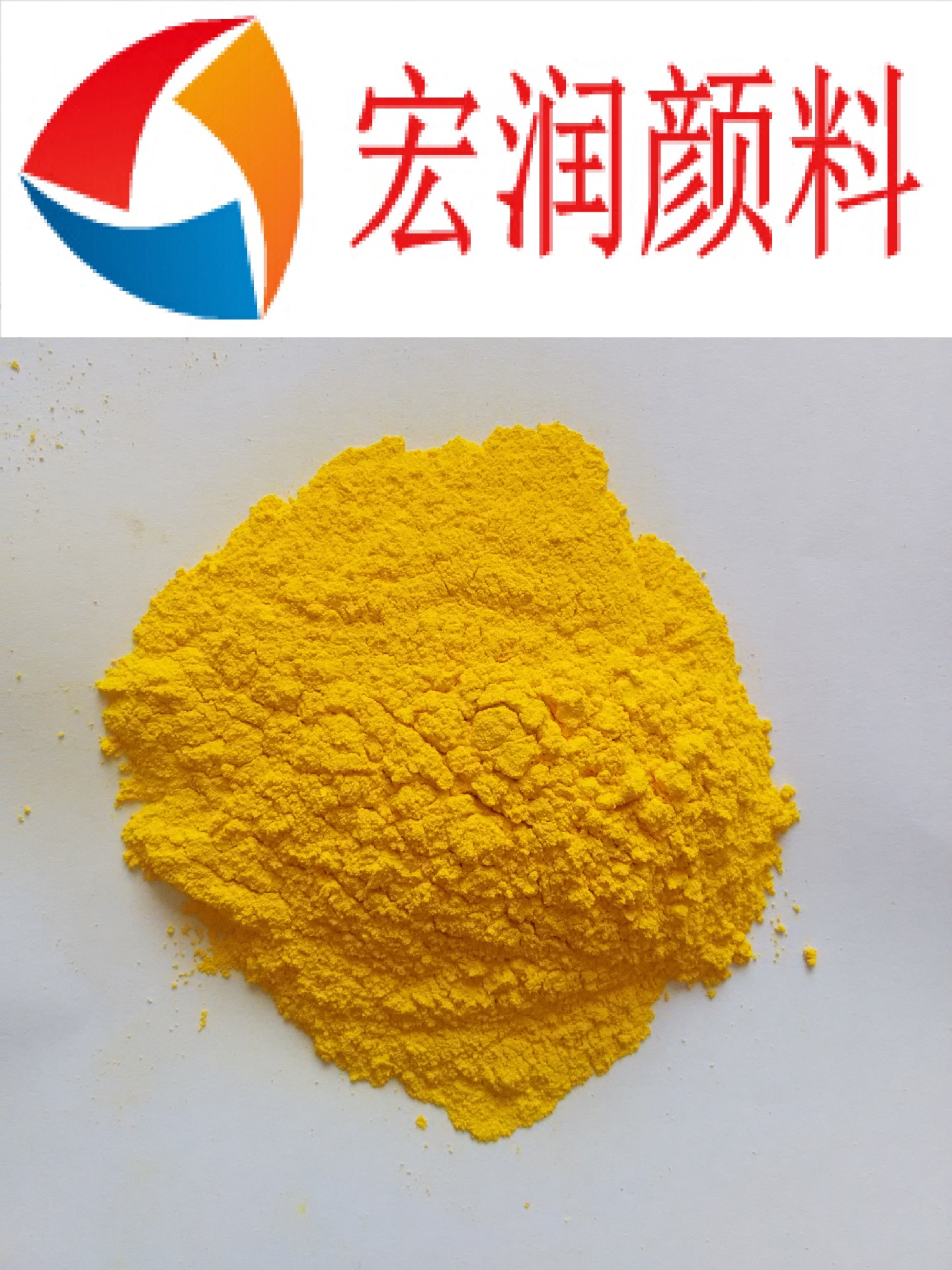
粉末涂料中易分散铝粉颜料的研究摘要:针对铝粉颜料在粉末涂料中高添加量的情况下分散效果不佳、抗电压 稳定性差、容易堵枪聚枪等缺点,对易分散铝粉颜料工业生产的关键技术进行了 研究。通过对树脂种类、树脂包覆量及反应时间的选择性研究,确定了易分散铝 粉颜料的生产工艺条件。以混合的活性树脂为包覆树脂,与致密硅包铝粉颜料的 质量比为 1:1 的情况下,反应4h 后,制得易分散铝粉颜料,并通过与处理前的 铝粉颜料对比,验证了该易分散铝粉颜料在添加量比较高的情况下,具有更优异 的分散性、抗电压稳定性以及更好的耐酸碱性。关键词:易分散铝粉颜料;活性树脂;表面处理;分散性0 引言伴随着环保压力日益增大,涂装工艺面临全新的挑战,粉末涂料、水性漆 高固分颜料、免喷涂等用铝粉颜料的需求日益高涨。在兼顾环保的同时,具有更 优秀的装饰效果和更好的防护性能,使用粉末涂料能达到仿油漆的应用效果也成 为了粉末涂料产业的新追求。粉末涂料具有无 VOC 排放100%成膜、漆膜更厚、漆膜性能优良、能耗低 生产效率高和可自动化涂装等优点,并在世界涂料和涂装行业中迅速发展。在粉末涂料中树脂和颜料是粉末涂料重要的组成部分,目前其主要有 3 种混 合工艺即挤出工艺、干混工艺以及邦定工艺[1]。
3 种混合工艺各有各的优势, 目前行业内更倾向于用邦定工艺生产粉末涂料,主要是因为它具有批次色差小 无花斑现象、颜料分散性好、回收粉可直接使用等优点。但是树脂与颜料在邦定 的过程中,由于机械剪切会对颜料表面原有的保护层产生一定程度的破坏,最终 会影响产品漆膜的耐候性能[2]。干混工艺具有设备简单、工艺简单,易控制 成本低、对漆膜破坏程度小等优点。由于金属颜料与底粉树脂有带电性能的差异,从而导致粉末涂料施工性差、容易产生花斑现象,尤其是在高添加量条件下容易 导致喷枪堵枪。使得该工艺金属颜料加入量严重受限,达不到油漆施工的漆膜效 果,其次金属颜料与底色粉容易分离,不利于粉末回收使用。为了解决上述问题,本研究通过对铝粉颜料表面包覆一层活性树脂,缩小颜 料与底粉树脂的带电性来提高颜料的分散性能[3]。由于铝粉颜料表面包覆了一 层树脂,使颜料与底粉的带电性接近,在粉末喷涂时由于带电性差异小,在工件 上吸附的颜料与底粉的比例接近,所以回收粉中的比例与原比例也接近,有利于 回收粉的循环使用。在成膜时,外层包覆的树脂会将铝粉颜料包裹且在漆膜表面 固化形成一层透明的膜,这层膜类似于油漆中清漆的作用,从而达到仿油漆的效 果。
由于在整个工艺过程中并未对颜料进行强机械剪切,所以该方法制备的产品 具有更优秀的耐候性能。1 实验部分1.1 原材料与试剂聚氨酯活性树脂(PU):广州杰合高分子材料有限公司;环氧活性树脂(E54): 恒远化工有限公司;丙烯酸活性树脂(GELB-L-1916):巴斯夫树脂科技有限公 司;芳香烃类(D60):岳阳巴陵精细化工有限公司;致密硅包铝粉颜料(ZPS-1030): 长沙族兴新材料股份有限公司;黑色底粉用环氧树脂 (E-20):爱粤金属粉末有限 公司;白色底粉用聚氨酯树脂(PU):华江粉末有限公司。以上均为工业级。1.2 易分散铝粉颜料工艺流程将致密硅包铝粉颜料在有机溶剂中分散均匀后,加入活性树脂,在一定条件 下,将铝粉颜料表面包覆一层树脂。通过这种方式来改良铝颜料表面特性,使致密硅包铝粉颜料与底粉树脂更加通过这种方式来改良铝颜料表面特性,使致密硅包铝粉颜料与底粉树脂更加通过这种方式来改良铝颜料表面特性,使致密硅包铝粉颜料与底粉树脂更加 亲和,缩短两者导电性能差异,使其能在高添加量的情况下也能很好静电喷涂亲和,缩短两者导电性能差异,使其能在高添加量的情况下也能很好静电喷涂亲和,缩短两者导电性能差异,使其能在高添加量的情况下也能很好静电喷涂[4]。
其工艺流程如图 1 所示。所示。1.3 易分散铝粉颜料的制备易分散铝粉颜料的制备1.3.1 铝粉颜料的表面处理铝粉颜料的表面处理将致密硅包铝粉颜料将致密硅包铝粉颜料与溶剂按质量比 1∶8加入包覆罐中,搅拌转速加入包覆罐中,搅拌转速 80r/min, 搅拌均匀后,控制温度 30~40℃30~40℃;缓慢加入与致密硅包铝粉颜料同等质量的活性;缓慢加入与致密硅包铝粉颜料同等质量的活性 树脂,搅拌均匀后,继续保持转速和温度搅拌,待反应树脂,搅拌均匀后,继续保持转速和温度搅拌,待反应 4h 后压滤,吹干成滤饼后压滤,吹干成滤饼 待烘干成粉[5]。1.3.2 烘干将吹干的滤饼,放入真空干燥箱中,调节烘烤温度将吹干的滤饼,放入真空干燥箱中,调节烘烤温度 70~90℃,烘干成粉。,烘干成粉。1.3.3 分散处理本研究采用机械分散处理,将烤干的颜料加入分散机中,将产品分散 8h 后, 备用。1.3.4 筛分将分散处理好的粉末产品加入筛分机中,用 150 目的筛网进行筛选,筛下物 即是易分散铝粉颜料 ZPBF1030S。1.4 分析与测试常规性能检测:根据 HG/T2456.2—2016 进行产品相关的检测。
粒度检测:取少量(0.5~1.0g)样品置于烧杯中,加入醇类溶剂,搅拌均匀。 放入超声分散机中分散 3~5min 后,采用欧美克激光粒度仪进行粒度的检测。静电喷涂检测:取一定量的铝粉颜料,再加入树脂底粉至 100g,充分摇匀 后进行静电喷涂。静电喷枪气压为 1.0MPa、静电电压为 80kV,枪口离铁板的距 离为 15cm,静电喷涂在马口铁板(20cm×10cm)上,然后放入200℃的烘箱中烘 烤 15min 后取出(涂层厚度为 60~80μm),目测漆膜并进行评价[6]。光泽测试:根据标准 ISO2813—2014,对漆膜进行光泽测试。耐酸碱性能测 试:根据 GB/T9274—1988 《色漆和清漆耐液体介质的测定》中的点滴法进行测 试。2 结束与讨论2.1 树脂种类的选择铝粉颜料表面包覆树脂的类型,会决定易分散铝粉颜料在粉末涂料中的应用铝粉颜料表面包覆树脂的类型,会决定易分散铝粉颜料在粉末涂料中的应用铝粉颜料表面包覆树脂的类型,会决定易分散铝粉颜料在粉末涂料中的应用 [7]。在相同条件下,用不同种类的活性树脂进行表面处理,然后对其烘干后的。在相同条件下,用不同种类的活性树脂进行表面处理,然后对其烘干后的。
在相同条件下,用不同种类的活性树脂进行表面处理,然后对其烘干后的 状态以及制成产品后的喷板进行对比,其结果见表状态以及制成产品后的喷板进行对比,其结果见表 1。由表 1 可知,在实验中,分别用环氧活性树脂、聚氨酯活性树脂、丙烯酸活可知,在实验中,分别用环氧活性树脂、聚氨酯活性树脂、丙烯酸活可知,在实验中,分别用环氧活性树脂、聚氨酯活性树脂、丙烯酸活 性树脂以及混合活性树脂对铝粉颜料进行包覆。烘干溶剂后,发现丙烯酸活性树性树脂以及混合活性树脂对铝粉颜料进行包覆。烘干溶剂后,发现丙烯酸活性树性树脂以及混合活性树脂对铝粉颜料进行包覆。烘干溶剂后,发现丙烯酸活性树 脂包覆的颜料成块状,比较难成粉;环氧活性树脂包覆的颜料也是成块,但是可脂包覆的颜料成块状,比较难成粉;环氧活性树脂包覆的颜料也是成块,但是可脂包覆的颜料成块状,比较难成粉;环氧活性树脂包覆的颜料也是成块,但是可 以捏碎成小片状;聚氨酯活性树脂和混合活性树脂包覆的颜料比较松散,呈粉末以捏碎成小片状;聚氨酯活性树脂和混合活性树脂包覆的颜料比较松散,呈粉末以捏碎成小片状;聚氨酯活性树脂和混合活性树脂包覆的颜料比较松散,呈粉末 状。在喷板后漆膜性能方面,混合活性树脂的制粉状态、平整性、清晰度、耐状。
在喷板后漆膜性能方面,混合活性树脂的制粉状态、平整性、清晰度、耐状。在喷板后漆膜性能方面,混合活性树脂的制粉状态、平整性、清晰度、耐候 性能、兼容性均优于其它树脂,因此本研究选择混合的活性树脂作为包覆用树脂。性能、兼容性均优于其它树脂,因此本研究选择混合的活性树脂作为包覆用树脂。性能、兼容性均优于其它树脂,因此本研究选择混合的活性树脂作为包覆用树脂。2.2 树脂的用量在相同条件下,改变混合活性树脂的用量,制成成品后,检测其光泽度。其在相同条件下,改变混合活性树脂的用量,制成成品后,检测其光泽度。其在相同条件下,改变混合活性树脂的用量,制成成品后,检测其光泽度。其 结果见图 2。由图2 可以看出,随着树脂包覆量的增加,光泽是不断增加的,但考虑到树可以看出,随着树脂包覆量的增加,光泽是不断增加的,但考虑到树可以看出,随着树脂包覆量的增加,光泽是不断增加的,但考虑到树 脂包覆量超过 50%,产品中的颜料含量会降低,此外达到相同包覆量的漆膜效果,,产品中的颜料含量会降低,此外达到相同包覆量的漆膜效果,,产品中的颜料含量会降低,此外达到相同包覆量的漆膜效果, 则需要加入更多的产品,制造成则需要加入更多的产品,制造成本会增加很多。
因此,选择树脂包覆量为本会增加很多。因此,选择树脂包覆量为 50%, 即与致密硅包铝粉质量比即与致密硅包铝粉质量比 1∶1。2.3 反应时间反应时间过短,则树脂没有全部包覆上去,易分散铝粉颜料性能会比较差,反应时间过短,则树脂没有全部包覆上去,易分散铝粉颜料性能会比较差,反应时间过短,则树脂没有全部包覆上去,易分散铝粉颜料性能会比较差, 粒径相对小一些。在相同条件下,改变不同反应时间,压滤后,通过检测压滤后粒径相对小一些。在相同条件下涂料品牌网,改变不同反应时间,压滤后,通过检测压滤后粒径相对小一些。在相同条件下,改变不同反应时间,压滤后,通过检测压滤后 溶剂中的不挥发物含量、产品得率以及粉末粒径来确定反应时间,结果见表溶剂中的不挥发物含量、产品得率以及粉末粒径来确定反应时间,结果见表溶剂中的不挥发物含量、产品得率以及粉末粒径来确定反应时间,结果见表 2。从表 2 中发现,在反应中发现,在反应4h 后,压滤后的溶剂中的不挥发物含量在缓慢下降。后,压滤后的溶剂中的不挥发物含量在缓慢下降。 烘干得粉率和粉末粒径的增加幅度不大,故混合的树脂在反应粉末粒径的增加幅度不大,故混合的树脂在反应 4h4h 时,反应比较 完全。
因此反应 4h 为最佳反应时间。为最佳反应时间。2.4 铝粉颜料包覆前后对比铝粉颜料包覆前后对比2.4.1 喷板色相对比喷板色相对比分别取 2.5g 5g 10g10g 15g 的ZPS1030 制成粉末涂料喷板,分别取制成粉末涂料喷板,分别取 5g 10g 20g 30g 的ZPBF1030S 制成粉末涂料喷板,目测漆膜,其结果如图制成粉末涂料喷板,目测漆膜,其结果如图制成粉末涂料喷板,目测漆膜,其结果如图 3 和图 4 (由 于 15g 的ZPS1030 制成的粉末涂料聚枪现象很严重,因此没有喷板)。制成的粉末涂料聚枪现象很严重,因此没有喷板)。制成的粉末涂料聚枪现象很严重,因此没有喷板)。从图 3 可以看出,随着可以看出,随着 ZPS1030 添加量的增加,色相变化不明显,而随着添加量的增加,色相变化不明显,而随着 ZPBF1030S 添加量的增加,遮盖力越来越好添加量的增加,遮盖力越来越好,色相越来越白。从图 4 可以看出,在铝含量为可以看出,在铝含量为 2.5%的情况下,由于包覆树脂后,的情况下,由于包覆树脂后,ZPBF1030S 的粒径增加了,所以ZPBF1030SZPBF1030S 的遮盖力反而比ZPS1030 的遮盖力要差,但是随的遮盖力要差,但是随 着铝含量的不断增加,ZPBF1030SZPBF1030S 的遮盖力越来越明显优于 ZPS1030ZPS1030 的遮盖力。
2.4.2 分散性对比记录上述静电喷涂过程中的现象和目视对比样板情况,并在同一记录上述静电喷涂过程中的现象和目视对比样板情况,并在同一记录上述静电喷涂过程中的现象和目视对比样板情况,并在同一样板上任意 取一点为标,对样板不同点打色差,测量取一点为标,对样板不同点打色差,测量 5 次,取色差最大的为记录值。详细结次,取色差最大的为记录值。详细结 果见表 3。由表3 可知,未处理过的原材料在添加量在可知,未处理过的原材料在添加量在 5%时,铝粉颜料开始有聚枪,时,铝粉颜料开始有聚枪, 随着添加量的继续增加,聚枪现象越来越严重,到随着添加量的继续增加,聚枪现象越来越严重,到 15%时,甚至出现了堵枪的现时,甚至出现了堵枪的现 象。而易分散铝粉颜料在添加量象。而易分散铝粉颜料在添加量 30%下,颜料也能通过干混也能稳定的静电喷涂下,颜料也能通过干混也能稳定的静电喷涂 且不堵枪口、色差较小、色相均匀无阴阳色,故颜料在漆膜中分散性好。且不堵枪口、色差较小、色相均匀无阴阳色,故颜料在漆膜中分散性好。且不堵枪口、色差较小、色相均匀无阴阳色,故颜料在漆膜中分散性好。2.4.3 不同电压下静电喷涂不同电压下静电喷涂将 ZPS1030 和 ZPBF1030SZPBF1030S 按添加量配成 100g 粉末涂料 3 份,分别在不同电份,分别在不同电 压(40KV60KV 80KV)下,进行静电喷涂,制备样板,并检测与)下,进行静电喷涂,制备样板,并检测与)下粉末涂料用铝粉,进行静电喷涂,制备样板,并检测与40KV 喷板的 色差,结果见表 4。
由表4 可知,ZPBF1030SZPBF1030S 在不同电压下,静电喷涂制备的样板色差小粉末涂料用铝粉,而在不同电压下,静电喷涂制备的样板色差小,而 ZPS1030 样板色差较大,所以样板色差较大,所以 ZPBF1030S 具有较好的抗电压稳定性。具有较好的抗电压稳定性。2.4.4 耐化学性能测试耐化学性能测试将 ZPS1030 和 ZPBF1030SZPBF1030S 分别采用邦定和干混的方法与底粉混合均匀(铝含分别采用邦定和干混的方法与底粉混合均匀(铝含 量保证为 5%),制成样板,分别检测耐酸碱性能,结果见表制成样板,分别检测耐酸碱性能,结果见表 5。由表5 可知,铝粉颜料的耐酸性没有明显变化,耐碱性能铝粉颜料在干混时, 包覆后的铝粉颜料明显有提高;而铝粉颜料在邦定后耐碱性能有所下降。易分散 铝粉在邦定后比致密硅包铝粉颜料的耐碱性能有所提高。以上表明 ZPS1030 是在 铝片表面包覆一层厚型的致密的二氧化硅保护层,具有优异的耐化学性能;而易 分散铝粉颜料 ZPBF1030S 是在铝粉颜料表面包覆一层活性的树脂,对耐化学性能 略有提高;对比邦定工艺,颜料在邦定过程中,由于机械剪切对颜料表面包覆层 破坏较大,导致漆膜的耐化学性能降低;但是经过易分散处理后,易分散铝粉颜 料用邦定制备漆膜也略好于直接邦定的粉制备的漆膜,表明包覆一层树脂能提高 颜料的耐剪切性能。3 结语通过对包覆树脂的种类、包覆树脂的用量、反应时间,确定了以混合的活性 树脂为包覆树脂,与致密硅包铝粉颜料的质量比为 1∶1 的情况下,反应 4h 后, 制得的易分散铝粉颜料有很好的抗电压性和耐酸碱性能,并且在高添加量的情况 仍然具有良好的分散性。